Revolutionizing EV Battery Production: Silane's Impact on Silicon-Anode Advancements
Vincent Pluvinage and George Schlowsky discuss the progress of anode technology within the EV battery industry.
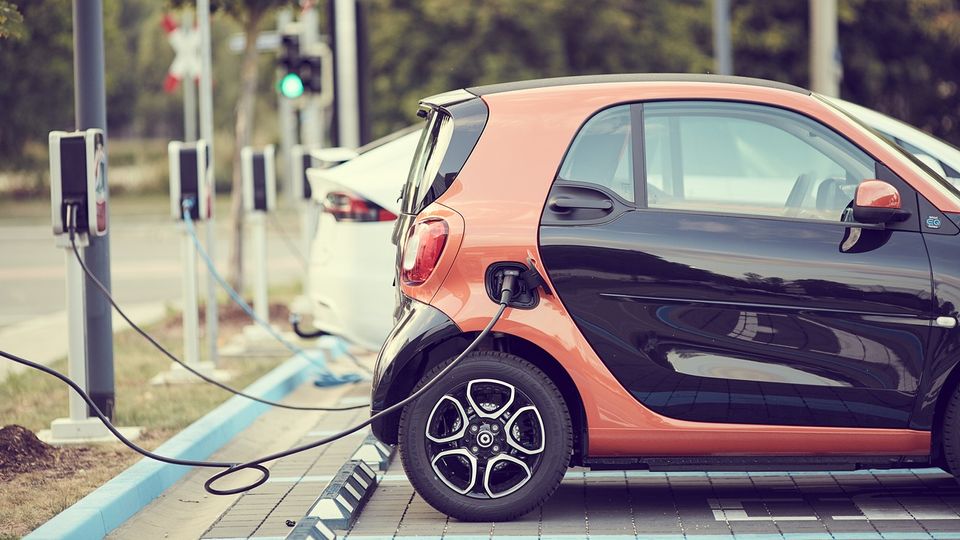
Complete the form below to unlock access to ALL audio articles.
The electric vehicle (EV) industry is at the forefront of a transformative shift towards sustainable transportation, with battery technology playing a pivotal role in driving this change.
Silicon, a promising material for EV batteries, offers increased energy density and range at a lower cost, but its widespread adoption faces manufacturing challenges. To address this, OneD Battery Sciences and Koch Modular Process Systems have joined forces in a strategic partnership to revolutionize EV battery production.
Technology Networks recently connected with Vincent Pluvinage, CEO of OneD Battery Sciences, and George Schlowsky, president of Koch Modular, to shed light on the advancements of anode technology within the EV battery industry.
This conversation follows the recent announcement of the OneD-Koch Modular partnership, aimed at scaling up silicon-graphite anode materials for the next generation of affordable EV batteries.
Anna MacDonald (AM): Can you give an overview of silicon in the EV battery industry and its manufacturing process?
George Schlowsky (GS): Silicon plays a crucial role in enhancing the energy density of EV batteries, which directly translates to increased range and reduced weight of electric vehicles. Traditionally, graphite has been the primary material used in anode electrodes, but incorporating silicon into the anode material can significantly boost battery performance. However, silicon's adoption has been hindered by its high cost and challenges in accessibility.
Koch Modular’s silane technology combats this challenge. The manufacturing process typically involves the production of silane gas (SiH4), the key precursor for silicon, followed by integrating silicon into graphite anode materials. Silane gas proves to be the most cost-effective method for refining silicon metal (referred to as MGS or metallurgical grade silicon, consisting of 99% silicon and 1% impurities).
It's a common understanding among graphite suppliers to EV cell factories that impurities must be removed to below 0.001% to prevent cell deterioration. Our silane technology is the world’s only electronics-grade modular silane plant that has been successfully operating for over a decade. We design and deliver the technology modularly, which significantly decreases capital costs and project timelines, enabling OneD’s SINANODE technologies to process and add silicon inside EV-grade graphite powders from industrial suppliers.
This reduces the overall cost of manufacturing an EV battery and allows OEMs to scale the production of more affordable EVs.
AM: What are the current challenges associated with battery manufacturing for EVs? How will the partnership between OneD Battery Sciences and Koch Modular benefit the battery industry, and what does that do to the supply chain?
Vincent Pluvinage (VP): Current challenges in battery manufacturing for EVs include high costs, limited scalability of silicon technologies and supply chain dependencies, particularly on critical materials like silane gas and EV-grade graphite. Many silicon technologies are too expensive and not scalable enough to support production of batteries for millions of affordable EVs.
The key silicon precursor, SiH4, is produced mostly in China, which is making over 93% of the global production of solar cells. Now, through OneD’s partnership with Koch Modular, silane will be produced in North America – allowing OEMs to take advantage of Inflation Reduction Act incentives and reduce dependencies on foreign entities.
This collaboration enables large-scale production of silicon-enhanced graphite anode materials, reducing costs, increasing production scalability and mitigating supply chain risks. Ultimately, this benefits the battery industry by providing customers with a higher performing EV battery at a reduced cost, allowing them to stay competitive in the market.
Additionally, since SINANODE is a globally-patented technology that can be deployed using existing suppliers across multiple continents. This eliminates the need for customers to reinvent their supply chain.
AM: Can you give a high-level overview of the technology behind the partnership?
VP: The partnership combines OneD's SINANODE technologies with Koch Modular's expertise in silane gas manufacturing. SINANODE utilizes a scalable and cost-effective manufacturing process to integrate nano-silicon directly into EV-grade graphite powders, eliminating the need for expensive carbon substrates.
Koch Modular's silane manufacturing expertise ensures the efficient silane gas production, a critical silicon precursor, supporting the large-scale production of silicon-enhanced graphite anode materials. By co-locating silane production plants with SINANODE processing facilities, the partnership optimizes production efficiency and reduces costs, leading to more competitive EV battery solutions.
AM: Where are you now with the project, and what updates can you provide?
GS: Currently, OneD Battery Sciences and Koch Modular are in the process of designing the first integrated North American plant to produce 20,000 tons of silicon-graphite anode material per year. This capacity will be sufficient for the batteries of approximately 1,000,000 EVs annually.
Additionally, OneD's SINANODE pilot facility in Moses Lake, WA, is set to go online in early 2024 to support the EV battery qualification process for OEMs. These developments signify significant progress towards establishing a robust and sustainable supply chain for silicon-enhanced graphite anode materials in the EV battery industry.
About the interviewees:
George Schlowsky is president of Koch Modular Process Systems. George is a chemical engineer with 58 years of experience in the process design of all types of chemical manufacturing plants. He has specific expertise in complex separations processes and equipment design, including distillation, liquid-liquid extraction, absorption and adsorption, crystallization, reactive distillation, organic synthesis, heat transfer and fluid flow, process control and instrumentation. George holds a B.S. in Chemical Engineering from Columbia University and an M.S. in Chemical Engineering from Virginia Polytechnic Institute.
Vincent Pluvinage is co-founder and chief executive officer of OneD Battery Sciences. After beginning his career at AT&T Bell Laboratories, Vincent became a successful serial entrepreneur. First by spinning out ReSound Corporation, then co-founding Preview Systems and IPValue Management, Inc. After leading the strategic acquisition and private equity team at Intellectual Ventures, Vincent founded Invention Capital Partners, then led the acquisition of the nanowire technologies and R&D team from Nanosys, to form OneD in 2013. Vincent holds degrees in Applied Physics (UCL, Belgium) and Bioengineering (PhD, University of Michigan) and is an inventor on more than a hundred patents.