Improving Battery Analysis With Simultaneous Rheology and Impedance Measurements
Sarah Cotts discusses how the Rheo-Impedance accessory can help to provide greater insights for battery scientists.
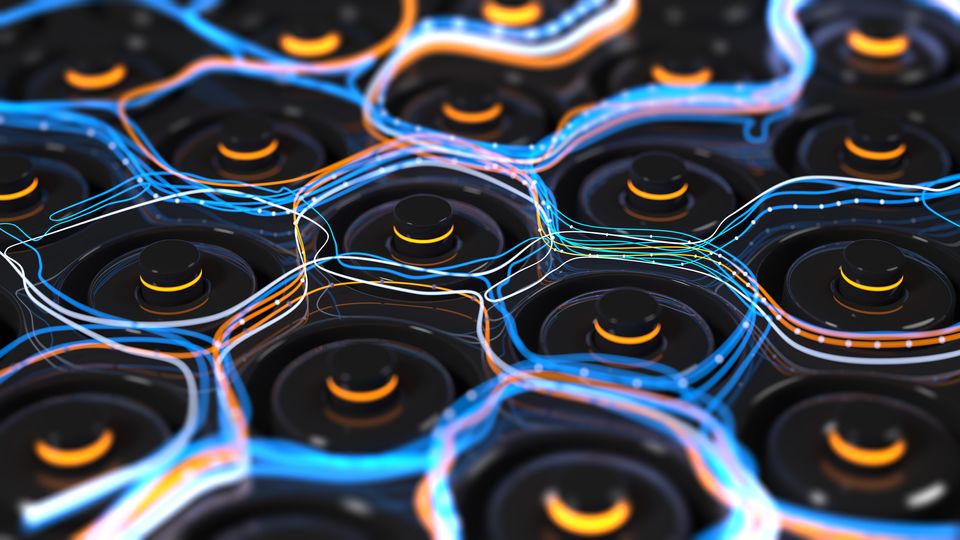
Complete the form below to unlock access to ALL audio articles.
At the recent International Battery Seminar in Orlando, Waters Corporation announced the Rheo-Impedance Spectroscopy accessory for its TA Instruments Discovery Hybrid Rheometers (HR). The new accessory enables simultaneous electrical impedance and rheological measurements to be carried out under real-world and process-relevant conditions, providing greater insights for battery scientists.
Technology Networks spoke to Sarah Cotts, principal product manager of flow properties within Waters-TA Instruments, to learn more about the Rheo-Impedance accessory and how it can help overcome limitations with current analysis approaches to improve battery development.
Anna MacDonald (AM): What are a few common challenges that the industry faces during battery development and manufacturing?
Sarah Cotts (SC): The battery industry continues to work to uncover the best materials and processes to drive efficiency and low-cost manufacturing. Battery electrodes (the cathode and anode) are typically manufactured by wet slurry processing. This involves mixing the electrode active materials, binder/additive and solvent into a slurry, then coating it on the metal current collector, drying to remove solvent and calendaring (compacting) the electrode.
It is essential to identify the optimal formulation and processing condition to produce a good electrode, which ultimately impacts battery performance. Variables are assessed at each step of the development process, including:
1) Quantity of active material, binder and conductive additive used,
2) Slurry mixing and coating process conditions,
3) Material change during processing and
4) Electrode electrochemical properties.
Electrode performance is difficult to predict at the material and slurry production stage, which often results in large amounts of electrode scrap after final electrode testing.
AM: Why do battery researchers study rheology and impedance, and what’s the value of measuring them simultaneously?
SC: Rheology is the science of deformation and flow. Knowing the rheological properties of a material allows researchers and manufacturers to predict the behavior of a slurry during mixing, storage, pumping and coating. The conductive additive plays an outsized role in determining the flow behavior of an electrode slurry. Carbon black is typically used to create an electrically conductive network from active material particles to the current collector. Carbon black also forms a structural network that breaks during flow and reforms when the slurry is at rest.
Impedance spectroscopy can be used to measure the conductive network and a rheometer can be used to measure flow properties and mechanical recovery of the slurry. When the two measurements are done simultaneously, flow-induced changes in the conductive network can be observed. Combined rheo-impedance experiments can reveal conductive additive distribution throughout the material, processing and flow impacts to the conductive network, and reformation duration of the electrical and mechanical network after high shear processes (like coating).
AM: What are the limitations of current rheology solutions?
SC: Rheological measurements provide a qualitative comparison of carbon black distribution but lack insights into the critical electrically conductive network. Battery materials scientists developing slurries spend significant time and resources reformulating and testing in situ to ensure network conductivity. But now, with impedance measurements incorporated with the rheometer, electrode slurries are no longer a “black box” – scientists can directly measure slurries’ conductive networks and accelerate development.
AM: Can you tell us more about the Rheo-Impedance accessory and how it overcomes these issues?
SC: Rheo-Impedance incorporates a dielectric measurement of the battery slurry with simultaneous rheology measurements. The distribution of conductive additives is reflected in both physical and electrical properties, and the ability to measure both simultaneously connects microstructure with rheological behavior. Most importantly, Rheo-Impedance enables measurements of electrical impedance under shear, replicating processing conditions. Conductive networks are highly shear-sensitive; it’s critical to evaluate the conductive network in the slurry not just after mixing, but also under shear deformation experienced during the coating process, ensuring the conductivity is maintained in the finished electrode.
The new Rheo-Impedance accessory announced by Waters Corporation for our TA Instruments Discovery HRs uses a unique, patent-pending technology accessing the full range of rheological measurements simultaneous with impedance, with no limitations to the Discovery HR’s rotational deformation or torque sensitivity.
AM: What does this innovation mean for the future of battery development and manufacturing?
SC: The Rheo-Impedance accessory enables scientists to better predict slurry behavior under processing conditions and the performance of the slurry’s electrically conductive network, which ultimately relate to the final electrochemical properties of the battery. Battery electrode slurry formulation and process development can be guided by Rheo-Impedance to speed up the development and scale-up process. The accessory can also be used for QA/QC to identify potential failure in the early stages of production to improve efficiency and reduce scrap.
AM: Where do you see the battery industry going in the next three to five years?
SC: I would expect innovation to drive the future of the battery industry. It is a rapidly growing industry with new technology in the market. The battery industry is aiming for higher energy density, safer batteries and more efficient manufacturing to drive battery performance up and costs down.
Sarah Cotts was speaking to Anna MacDonald, Senior Science Editor for Technology Networks.
About the interviewee:
Sarah Cotts is the principal product manager of flow properties within Waters-TA Instruments, supporting the Discovery Hybrid Rheometer product development, marketing and applications across a broad range of industries.